Power generation in white cement plants from waste heat …
Waste heat recovery systems are developed in cement plants to utilize the waste heat discharged from the production process. Waste heat is converted into electricity without additional fuel consumption, which means that CO 2 emissions would be reduced.
اقرأ أكثر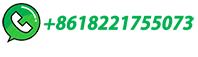
Cogenerationof Power Utilising Waste Heatin Cement …
The document discusses cogeneration of power in cement plants using waste heat. It states that nearly 40% of total heat input in dry cement plants is lost as waste heat from preheaters and coolers, which can be utilized to generate electricity. Cogeneration can help meet power demands, conserve energy, and reduce greenhouse gas emissions. Technologies based on …
اقرأ أكثر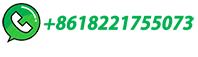
Full article: Energy conservation and waste utilization in the cement
For a typical cement plant capacity of 210 ton/h, up to a total of 166,000 tons of municipal waste can be burnt in the kiln per day at a rate of 20.96 ton/h to achieve the same temperature profile as when the plant operates on petcoke. ... "Energy Balance and Cogeneration for Cement Plant." Applied Thermal Engineering 22 (5): 485–494 ...
اقرأ أكثر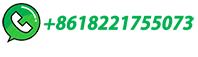
Using waste energy from the Organic Rankine Cycle cogeneration …
The analysis of mass and energy balances of a typical rotary kiln cement plant is performed in this paper. The objectives are to evaluate the mass and energy balances in the cement plant, in order to determine the overall energy efficiency of the process and to enable their recovery by installing an ORC plant cogeneration system. 2.
اقرأ أكثر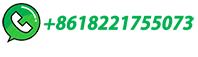
Crockett Cogeneration Project | California Energy …
The Crockett Cogeneration Project (CCP) is located in the unincorporated area of Crockett, Contra Costa County, within the C&H Sugar Refinery (C&H) compound, which consists of an extensive industrial complex containing large brick, steel, and concrete buildings, a steel conveyor system, wooden wharf, large bulk sugar storage bins, and a flue gas stack for the …
اقرأ أكثر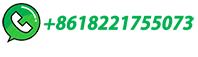
Sustainable Waste Management: A Case Study of …
Cement plants are an essential part of India's industrial landscape and are increasingly important partners in innovative waste management solutions, called co-processing. Co-processing waste in this way consists of using both the calorific potential to heat the kiln and the material component from the fuel ash as a raw material, It also has ...
اقرأ أكثر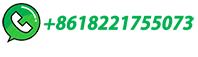
A CASE STUDY: THE WASTE HEAT RECOVERY AND …
emissions. In existing plants cogeneration technologies based on bottoming cycles have potential to generate up to 15-30 percent of the power requirement of a plant. Such a development …
اقرأ أكثر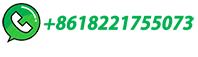
Electricity Cogeneration Potential in Minas Gerais Cement …
To assess the electricity cogeneration potential in the Minas Gerais cement industry with thermodynamic cycles is the main purpose of this study. The potential was estimated based on Minas Gerais cement sector data. The Kalina cycle, the organic Rankine cycle, and the conventional Rankine cycle were technically and economically assessed.
اقرأ أكثر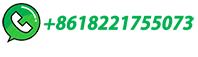
Cement Plant Cogeneration Opportunities
Cement Plant Cogeneration Opportunities Abstract: Rapid escalation of energy costs during the seventies requires a serious investigation of ways to reduce the industrial energy bill which has more than doubled in many states since 1977. Cogeneration offers one way of improving the efficiency of energy utilization for the cement industry.
اقرأ أكثر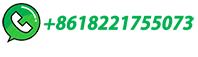
(PDF) Waste Heat Recovery Power Generation Systems for Cement …
A typical 3,000 tonne of clinker per day capacity plant produces 130,000 and 170,000 Nm 3 /h of grate cooler air and kiln exhaust, respectively.
اقرأ أكثر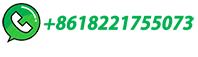
List of Cement Factories Carrying Out Co Processing …
Hume Cement Sdn. Bhd. Lot 300254, 300255, 300256 Mukim Teja, Daerah Kinta, 31610 Gopeng, Perak: Pn. Serina Ho Chia Yu Manager, Sustainability Tel: 016-3512828 E-mel: [email protected]: 6. Perlis. Negeri Sembilan Cement Industries Sdn Bhd Bukit Ketri, Mukim of Chuping 02450 Kangar, Perlis: Pn. Hani Adzlin Ad'nan Environmental Officer Tel ...
اقرأ أكثر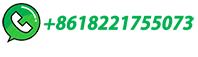
Case Studies in Thermal Engineering
cement plant cogeneration is less than 1.5 years. In existing plants cogeneration technologies based on bottoming cycles have potential to generate up to 25–30% of the power requirement of a plant.
اقرأ أكثر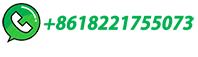
Cogeneration | PPT
3. NEED FOR COGENERATION Thermal power plants are a major source of electricity supply in India. In conventional power plant, efficiency is only 35% and remaining 65% of energy is lost. The major source of loss in the conversion process is the heat rejected to the surrounding water or air due to the inherent constraints. Also further losses of around 10-15% …
اقرأ أكثر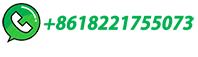
(PDF) Electricity Cogeneration Potential in Minas Gerais Cement …
The electricity cogeneration potential in the Minas Gerais cement industry is near 100 MW, and it is in the south-central region of Minas Gerais, where there is a greater population and energy ...
اقرأ أكثر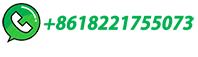
Waste Heat Recovery in Cement plant
consumption in cement production process, the recovery waste heats can be achieved in order to produce the electrical energy by utilization cogeneration power plant. This means no additional fuel consumption and thus, nergy and the emissions of greenhouse gases. In …
اقرأ أكثر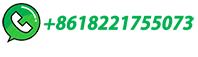
Exergy analyses and parametric optimizations for different …
In order to recover waste heat from the preheater exhaust and clinker cooler exhaust gases in cement plant, single flash steam cycle, dual-pressure steam cycle, organic …
اقرأ أكثر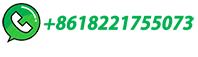
Performances Optimization and Comparison of Two Organic …
In this paper, the potential application of Organic Rankine Cycle (ORC) for cogeneration in a cement plant is presented. Two ORC system configurations are considered.
اقرأ أكثر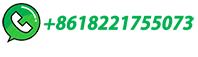
Heat Integration in a Cement Production | IntechOpen
1. Introduction. Nowadays, cement manufacturing is an energy-intensive industry. The energy costs of cement industry are about 40% of the product cost that indicates that this sector is one of the biggest CO 2 emitter. The global anthropogenic CO 2 emission of cement industry is approximately 5% [].The International Energy Agency reported in 2011 that the …
اقرأ أكثر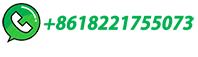
Using waste energy from the Organic Rankine Cycle cogeneration …
The analysis of mass and energy balances of a typical rotary kiln cement plant is performed in this paper. The objectives are to evaluate the mass and energy balances in the cement plant, in order to determine the overall energy efficiency of the process and to enable their recovery by installing an ORC plant cogeneration system. 2.1.
اقرأ أكثر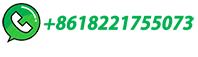
Energy balance and cogeneration for a cement plant
The cement industry is one of the most intensive energy and cost industries in the world that consumes about 3800 MJ per tonne of cement produced.
اقرأ أكثر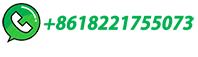
Waste Heat Recovery | ORC Heat Recovery
The integration of cogeneration in ORC plants further optimizes energy efficiency by simultaneously producing electricity and useful heat, which can be utilized in various industrial processes. ... TURBODEN DIRECT EXCHANGE HEAT RECOVERY ORC SYSTEM FOR CEMENTIROSSI CEMENT PLANT TURBODEN SOLUTIONS FOR INDUSTRIAL …
اقرأ أكثر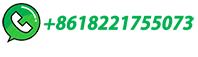
Exergy analyses and parametric optimizations for different …
The cogeneration power plants in cement plant can recover the waste heat available from the preheater exhaust and clinker cooler exhaust gases and generates …
اقرأ أكثر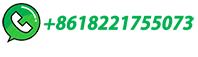
Thermodynamic analysis and cogeneration of a cement plant …
The analysis can be used as a precursor to achieve the basic objectives of any cement plant i.e. minimizing energy consumptions, minimizing the cost of production, and maximizing plant productivity.
اقرأ أكثر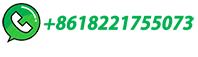
Sand & Cement Cogeneration Plant,
Sand & Cement Cogeneration Plant. ... Sand and cement cogeneration production line is broadly used in crushing all kinds of ores and enormous stones into middle-fine particles. Concrete crushing plant can also be broadly utilized in mining business, metallurgy, creating materials, sub way, railway, h2o conservancy and chemical industry. ...
اقرأ أكثر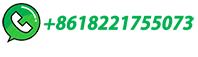
Decarbonization In Cement Plants With Waste Heat …
emissions In Cement Plant 4 56% 12% 32% CO2 emitted from calcination process CO2 emitted from electricity CO2 emitted from fuels The calcination process in Kiln and precalciner accounts for ~0.37 tCO2/t cement Fuel (Coal & Petcoke) accounts for ~0.21 tCO2/t cement Electrical energy consumption of the complete plant accounts for ~0.08 tCO2/t cement
اقرأ أكثر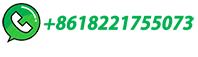
Use of fly ash from a cogeneration plant in concrete
It was found that for less than 28 days of curing, the concrete with up to 30% cogeneration plant fly ash can have a compressive strength 10% lower than the regular concrete. However, over that curing period, the situation was reversed and the former has significantly more compressive strength than the latter. The compressive strength of ...
اقرأ أكثر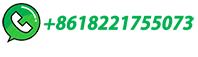
A CASE STUDY: THE WASTE HEAT RECOVERY AND …
of cement and typical requirements for electrical energy use is in the range of 80-125 kW hr per metric tons of cement. Cogeneration systems have been successfully operating in cement plants in India, China and South-east Asian countries. WHRPG technology started from the late 1960s in Europe and
اقرأ أكثر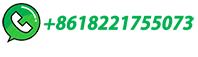
(PDF) Waste Heat Recovery Power Generation …
This paper is an introduction to Waste Heat Recovery Generation (WHRG) systems, their operations and feasibility for cement production process also a review of four common power generation...
اقرأ أكثر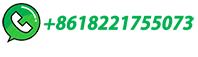
Low carbon measures for cement plant – a review
Cement manufacturing is an energy and carbon-intensive industry. The cement industry contributes approximately 5% of the global man-made carbon dioxide (CO 2) emissions and is thus becoming the second largest CO 2 contributor in industry after power plants. A wide range of options are available to considerably reduce CO 2 emissions. This paper reviewed …
اقرأ أكثر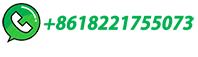
On the rise: Building and waste heat recovery at Najran Cement
Table 1: Capacities and suppliers of major equipment to be installed on Najran Cement's Line 3 at Sultana in the south of KSA. Waste Heat Recovery (WHR) power project. In addition to the Line 3 cement project and CPP, NCC intends to play a pivotal role in KSA by reducing CO 2 emissions, optimising cement plant operation to improve energy efficiency and …
اقرأ أكثر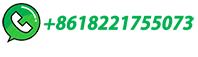