Comprehensive Study on the Mechanism of Sulfating Roasting …
The sulfating roasting at 600 °C during 180 min with the optimal Fe2(SO4)3∙9H2O addition followed by water leaching enables to recover 99% Zn and 80.3% Cu, while Fe, Pb, Ag, In, Ga retained almost fully in the residue. Zinc plant residue (ZPR) is a secondary material generated during hydrometallurgical zinc production that contains considerable contents of …
اقرأ أكثر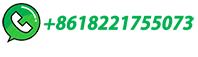
A new approach of aluminum extraction from drinking water …
This study has looked into the physico-chemical and mineralogical characteristics of the raw DWTS resulting from the drinking water treatment plant (DWTP), in order to elucidate the matrix's reactivity with (NH 4) 2 SO 4 as an extractant and to determine the effectiveness of the process to extract Al as a function of roasting parameters ...
اقرأ أكثر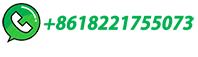
Spodumene Acid Roasting Kilns & Process …
Spodumene concentrate is mixed with sulfuric acid and roasted as part of the conversion to lithium compounds. THE ACID ROASTING PROCESS. Acid roasting is carried out through calcination in a rotary kiln at temperatures …
اقرأ أكثر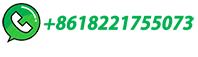
Sustainable Copper Production Based on Fluid-Bed …
The fluid-bed processes utilized are partial, sulfate-producing, and dead roasting. The focus of this paper considers the advantages of the dead-roasting process.
اقرأ أكثر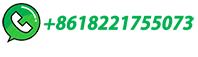
Self-sulfidation roasting and flotation of electroplating …
The effects of roasting temperature on the sulfidation ratio of copper and nickel and the volatilization ratio of zinc are shown in Fig. 4 (a). When the roasted temperature increased from 900 ℃ to 1050 ℃, the sulfidation ratio of copper and nickel increased from 38.78 % to 82.80 % and 81.97 % to 97.39 %, respectively.
اقرأ أكثر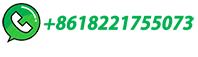
Recovery of Copper from Copper Sulfide Concentrate by Sulfation Roasting
Sulfation roasting was studied to extract copper from the copper sulfide concentrate. Sodium sulfite was added as sulfation agent to the copper sulfide concentrate during roasting in this study.
اقرأ أكثر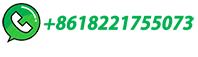
A Comparison Study on the Recovery of REEs from Red Mud …
In this study, the recovery of rare earth elements (REEs) from red mud (bauxite residue) was explored through a combination of citric acid leaching and sulfation roasting–water leaching processes, introducing an innovative approach to the field. The research uniquely investigates the influence of citric acid on the leaching behavior of REEs and impurities in both …
اقرأ أكثر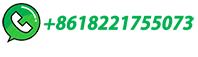
OneMine | Pilot
The design, operation, and performance of an integrated pilot plant for recovering zinc and copper from a complex sulfide ore are described. Metallurgical processing comprised selective sulfate roasting in a fluid bed, leaching in a weak sulfuring acid solution, recovering copper by cementation with scrap iron, air oxidation to remove soluble iron, more-or-less conventional …
اقرأ أكثر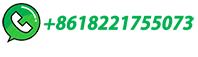
Study of Sulphatizing Roasting Process Using Iron Sulphates …
The possibility of metals recovery from zinc ferrite residues using transformational roasting processes was examined by roasting zinc ferrite residue from Doe Run Peru's La Oroya plant (Peru ...
اقرأ أكثر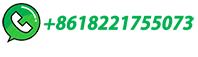
SULFATE ROASTING COPPER-COBALT SULFIDE …
The design of the commercial-scale sulfate roast ing plant at Jadotville was aimed at having a unit to 1) roast 80 metric tons of concentrates per day, on a dry basis, 2) fit into the larger plant required by 1959, and 3) have sufficient flexibility to roast a variety of concentrates under a variety of condi ...
اقرأ أكثر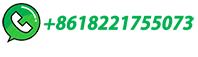
Preparation of ultrafine α-Al2O3 powder from fly ash by …
(NH 4) 2 SO 4 roasting technology was used for extracting alumina from fly ash which located in Shandong Zibo power plant. The roasting temperature, the mole ratio of Al 2 O 3 to (NH 4) 2 SO 4 and roasting time on the effect of the extraction rate of alumina was studied. The optimal roasting technology condition is 380°C for 120min with mole ratio of Al 2 O 3 to …
اقرأ أكثر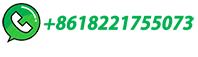
High-Zinc Recovery from Residues by Sulfate Roasting and …
The effects of the roasting and leaching parameters on zinc recovery were investigated. A maximum zinc recovery rate of 90.9% was achieved for a mixture with a ferric sulfate/residue weight ratio of 0.05 when roasting at 640°C for 30 min before leaching with water at room temperature for 20 min using a liquid/solid ratio of 10.
اقرأ أكثر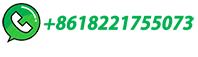
Recovery of valuable metals from zinc leaching residue by …
Then the metal sulfates can be easily separated from the sludge with water leaching, leaving a detoxified residue. And the sulfate roasting and water leaching processes were optimized. 2 Experimental 2.1 Materials and analysis Zinc leaching residue used in this work was provided by a zinc hydrometallurgical plant in Hunan Province, China.
اقرأ أكثر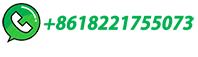
Extracting Lithium
The amount of lithium volatilized during potassium chloride-calcium sulfate roasting and during calcium sulfate roasting is the same (see table for calcium sulfate roast), but the amount of lithium extracted by water-leaching the calcines produced is 67 pct from the multiple-reagent roast as contrasted to 59 pct from the calcium sulfate roast.
اقرأ أكثر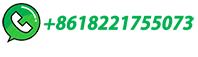
Comprehensive Study on the Mechanism of …
the roasting of zinc plant residue (ZPR) with iron sulfates. The study presents the results. of multifactorial research of the effect of temperature, r oasting time and amount of iron.
اقرأ أكثر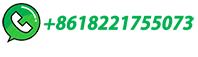
SULFATION ROASTING AND LEACHING OF SAMARIUM …
an acid plant. Net present value after five-years with an acid plant is $2.2 million whereas the project is unfeasible without sulfur recovery. This is based on a two stage roasting process and treatment of 1000 tonnes per year of samarium-cobalt magnet waste. Based on the success of the results from
اقرأ أكثر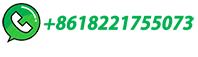
Comprehensive Study on the Mechanism of Sulfating Roasting …
Zinc plant residue (ZPR) is a secondary material generated during hydrometallurgical zinc production that contains considerable contents of valuable elements such as Zn, Cu, Fe, Pb, Cd, Ag, In, Ga, Tl. ... The sulfating roasting at 600 °C during 180 min with the optimal Fe 2 (SO 4) 3 ∙9H 2 O addition followed by water leaching enables to ...
اقرأ أكثر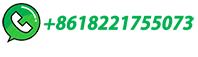
Extraction of alumina from high-alumina fly ash by …
roasting process were discussed. The experimental results showed that the leaching rate of alumina in the roasted material achieved 93.57% with the roasting temperature of 673 K, the roasting time of 60 min, and the mass ratio of ammonium sulfate to high-alumina fly ash of 6:1. The roasting kinetics
اقرأ أكثر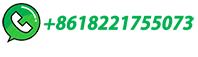
OneMine | Pilot
The design, operation, and performance of an integrated pilot plant for recovering zinc and copper from a complex sulfide ore are described.
اقرأ أكثر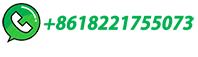
Journal articles on the topic 'Sulfation roasting'
Most of the oxides were converted to their respective sulfates during sulfation. By roasting, unstable sulfates (mostly iron) decomposed into oxides, while the REE sulfates remained stable. Roasting above 600 °C induces the formation of oxy-sulfates that are almost insoluble during AOL. Dissolved REEs precipitate after 7 days at room temperature.
اقرأ أكثر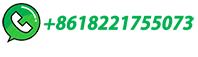
Sulfatizing roasting
Sulfatizing roasting Sulfation Roasting. Acid roasting technology (Fig. 2) rehes on differences in the volatiUty of the tetravalent oxides of selenium and tellurium at roasting temperatures of 500—600°C to selectively volatilise selenium from slimes. Acid roasting uses sulfuric acid as the oxidant for the conversion of selenium/selenides and tellurium/teUurides to their respective ...
اقرأ أكثر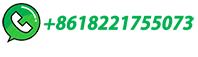
Extraction of vanadium from vanadium slag by sodium roasting …
The sodium roasting process uses sodium salt (Na 2 CO 3, NaCl, Na 2 SO 4) to transform spinel to soluble sodium vanadate (NaVO 3, Na 3 VO 4, Na 4 V 2 O 7) [6], [13], [14]. After roasting, the sodium vanadate is leached by water and vanadium-containing leachate is precipitated with ammonium and then calcined to obtain the V 2 O 5 product.
اقرأ أكثر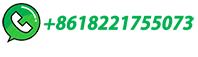
Lithium Production Processes
Such an acid-roast process was also used in a commercial plant operated by Lithium Corporation of America (acquired by FMC Corporation in 1995) to produce lithium carbonate between 1956 and 1998. 2 Nemaska Lithium Inc. (Canada) has recently reported a new acid-roast process for simultaneously producing LiOH·H 2 O and Li 2 CO 3 using …
اقرأ أكثر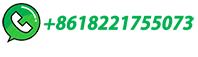
Unveiling the lithium deintercalation mechanisms in spent …
Sulfation roasting is a promising approach due to its excellent extraction of metal efficiency, cost-effective reducing agents, and the elimination of acid or alkali leaching agents. ... Spent LCO batteries were obtained from a waste treatment plant in the Chinese province of Chongqing. Pyrite was obtained from the Chinese company Guangxi ...
اقرأ أكثر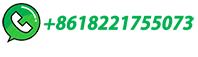
Recovery of Manganese by Roasting-Ammonia Leaching …
Heindl R, Ruppert J, Skow M, Conley J (1955) Manganese from steel-plant slags by a lime-clinkering and carbonate-leaching process: part I, laboratory development (in two parts). BuMines Rep Inv 5124:98. ... In this study, low-grade manganese carbonate ores were treated by roasting-ammonia leaching method. The effects of roasting...
اقرأ أكثر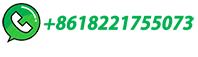
A Comparison Study on the Recovery of REEs from Red Mud …
In this study, the recovery of rare earth elements (REEs) from red mud (bauxite residue) was explored through a combination of citric acid leaching and sulfation roasting–water leaching processes, introducing an innovative approach to the field. The research uniquely investigates the influence of citric acid on the leaching behavior of REEs and impurities in both untreated red …
اقرأ أكثر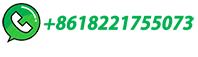
Sulfatizing Roasting and Leaching of Cobalt Ores at …
The Outokumpu Oy Cobalt Plant processes nickel, copper, and zinc bearing cobaltiferrous pyrite concentrate. Main operations: sulfatizing roasting, leaching, solution …
اقرأ أكثر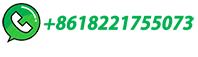
Processes | Free Full-Text | Comparison of the Preparation
Action Date Notes Link; article xml file uploaded: 6 November 2022 12:27 CET: Original file-article xml uploaded. 6 November 2022 12:27 CET: Update-article pdf uploaded.
اقرأ أكثر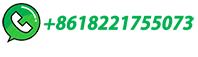
Roasting Solutions
Dead roasting is the most commonly used roasting process and is mainly applied in our zinc and pyrite roasters. When using a dead-roasting process for concentrates, the sulfides are completely transformed into oxides. The gas temperature in this type of …
اقرأ أكثر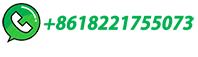
Extraction of alumina from high-alumina fly ash by …
The experimental results showed that the leaching rate of alumina in the roasted material achieved 93.57% with the roasting temperature of 673 K, the roasting time of 60 min, and the mass ratio of ammonium sulfate to high-alumina fly ash of 6 : 1.
اقرأ أكثر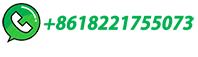