Iron ore dust scrubbing – Multi-vortex Wet Air …
The best choice for scrubbing heavy non-explosive dust, like iron ore dust, is wet air scrubbing. Compared to traditionally used dry scrubbing systems, wet air scrubbers provide benefits that have a significant positive effect on the …
اقرأ أكثر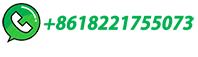
Dry Processing V S Wet Processing Of Iron Ore
I03 cement June 2024 GS gct . of calcium carbonate and clay iron ore sand or shale as a source of silica alumina and iron oxide The raw materials is crushed ground and mixed to obtained a between wet and dry process is the mix preparation method prior to …
اقرأ أكثر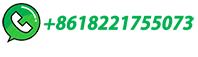
Numerical study of the dynamic behaviour of iron ore …
Iron ore wet granulation in a rotary drum has been simulated using DEM to understand the dynamics of iron ore particles during the granulation process. In the DEM programming, each particle's surface liquid content was quantified by a parameter of λ defined as the water/particle volume ratio (vol%).
اقرأ أكثر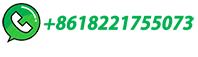
Iron ore beneficiation | Commodities | Mineral …
Incorporating crushing, grinding, classification, and gravity separation as well as high and low intensity magnetic separation across wet and dry applications for fine iron ore beneficiation.
اقرأ أكثر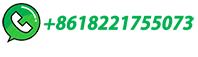
Modification of Wet Granulation Process During Iron Ore …
Sintering is an agglomeration process that fuses iron ore fines, fluxes, recycled products, slag-forming elements and coke. The purpose of sintering is to obtain a product with suitable ...
اقرأ أكثر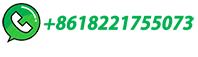
Process for iron ore pellets production
The present invention concerns a process for iron ore pellets production comprising at least one iron ore crushing stage in a roller press for the production of iron ore pellets. The crushing stage(s) can be done prior or after grinding, or still defined by successive passages of the material through the foregoing crushing stage.
اقرأ أكثر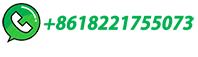
In-process control of manganese dithionate in the manganese ore …
Manganese ore-based wet flue gas desulfurization (MFGD) is a resourcing technology capable of simultaneously reutilization flue gas sulfur dioxide (SO 2) and green, low-carbon manganese leaching.However, the by-product manganese dithionate (MnS 2 O 6) greatly affects the use of desulfurization liquid.In this study, the iron introduced MFGD process to …
اقرأ أكثر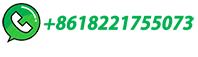
The Sintering Process of Iron Ore Fines – IspatGuru
The Sintering Process of Iron Ore Fines. Sintering plants are normally associated with the production of hot metal in blast furnaces in integrated steel pants. ... Cold and wet zone – It includes the zone of the sinter bed with a temperature of less than 100 deg C. This area is formed by the charge mix to be sintered, with upper limit ...
اقرأ أكثر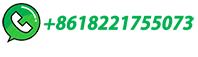
A study on plasticity and compression strength in wet iron ore …
The compression strength in wet iron ore green pellets is described in earlier textbooks [1], [3], [4], [5] by the well-known capillary theory and the Rumpf equation (Eq. ... The importance of green pellet plasticity for the iron ore balling …
اقرأ أكثر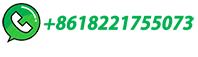
Iron ore crushing and screening process
The iron ore processing and production process mainly includes three processes: crushing, grinding and beneficiation. In the crushing process, the three-stage closed-circuit crushing is more modern and suitable for high-hardness iron ore crushing and can complete the work of ore crushing and partial dissociation, thereby improving the subsequent grinding …
اقرأ أكثر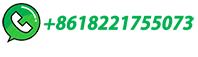
Beneficiation of Iron Ore
Beneficiation of Iron Ore and the treatment of magnetic iron taconites, stage grinding and wet magnetic separation is standard practice. This also applies to iron ores of the non-magnetic type which after a reducing …
اقرأ أكثر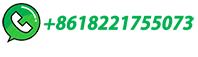
Iron Ore Magnetic Separation
The Chateangay; Ore & Iron Co., at Lyon Mountain, N. Y., the Empire Steel & Iron Co. and the Ringwood Co. in New Jersey, also use the dry process successfully. The Grondal wet separators have been recently installed at the Benson mines in New York. The largest development of the, wet process in this country is on the Cornwall ore at Lebanon, Pa.
اقرأ أكثر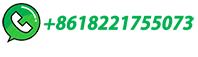
The six main steps of iron ore processing
The haematite ore in South Africa is processed in a dry process to a HQ lump ore with 64 % iron content and a sintered fine ore with 63.5 % iron content. For fine ore beneficiation, wet …
اقرأ أكثر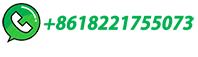
Iron Ore Screening
Iron ore screening equipment from Multotec is made from polyurethane or rubber screening media.Our screening equipment is ideal for high, medium or low grade profiles, reduce plant footprint by more than 33% and materials of construction ensure a long life at reduced cost with low maintenance requirements. Our polyurethane and rubber iron ore screening solutions …
اقرأ أكثر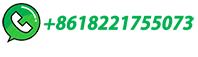
Modification of wet granulation process during Iron ore …
The sintering process can be defined as a thermal agglomeration process that is applied to a mixture of iron ore fines, recycled ironmaking products, fluxes, slag-forming agents, and solid fuel ...
اقرأ أكثر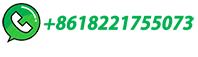
Exploring Low-Grade Iron Ore Beneficiation Techniques: A
Low-quality iron ore beneficiation is an essential process in the utilization of iron ore deposits, particularly as demand for iron and its alloys continues to rise due to rapid …
اقرأ أكثر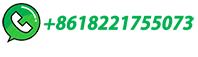
Modification of Wet Granulation Process During Iron Ore …
Sintering is the most extensively used and economic agglomeration process to prepare iron ore fines for blast furnace use. Granulation is the most critical factor controlling iron ore sintering process, as it improves sinter mix permeability. Currently, sinter plants are receiving significant proportion (up to 40%) of − 150 μm micro-fines in iron ore fines, which makes …
اقرأ أكثر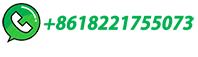
Beneficiation of Iron Ore
Beneficiation of Iron Ore and the treatment of magnetic iron taconites, stage grinding and wet magnetic separation is standard practice.This also applies to iron ores of the non-magnetic type which after a reducing roast are amenable to magnetic separation. All such plants are large tonnage operations treating up to 50,000 tons per day and ultimately requiring …
اقرأ أكثر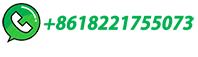
Iron Ore Beneficiation
Dry processing of iron ore presents an opportunity to eliminate costs and wet tailings generation associated with flotation and wet magnetic separation circuits. STET has evaluated several iron ore tailings and run of mine ore samples at …
اقرأ أكثر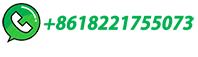
Vale to invest 11 billion reais in dry iron ore processing over …
In Carajás, as the iron content is already high (above 64%), the ore is only crushed and sieved, so it can be classified by size (granulometry). In Minas Gerais, the average content is 40% iron, contained in rocks known as itabirites. To increase the content, the ore is concentrated by means of wet processing (with water).
اقرأ أكثر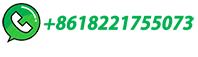
Modelling Cohesion and Adhesion of Wet, Sticky Iron Ores …
Wet sticky iron ore poses particular difficulties in every aspect of the material handling process. Material hang-ups in bins, pipes and chutes; carry-back and spillage due to insufficient belt cleaning; clogging of screens; malfunctioning of crushers as well as rat holing of gravity reclaimed stockpiles are all predominantly due to the inherent cohesion and adhesion characteristics of …
اقرأ أكثر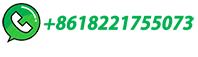
1. NOAMUNDI IRON MINE, M/s TATA STEEL LTD
Effective Ore Handling Plants: In Noamundi Iron Mine, two beneficiation circuits wet and dry are in operation Another step taken towards mineral conservation is the installation of Jigging plant and Hydro cyclone in the wet process for further beneficiation of …
اقرأ أكثر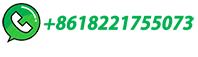
Iron ore beneficiation: an overview
The quality of Indian iron ore resources is generally good with high iron content and high percentage of lumpy ore. More than 85% of the hematite ore reserves are of medium- to high-grade (+62% Fe) and are directly used in blast furnace and in direct-reduced iron (DRI) plants in the form of sized lump ore, agglomerated sinter, and agglomerated pellets (Iron and …
اقرأ أكثر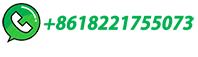
iron ore wet grinding process – Grinding Mill China
Pelletizing Process plant used circuit wet-grinding system …. Pretreatment process.In this process, the iron ore is ground into fines having qualities required for the subsequent balling process. …A wet grinding system … » More detailed Iron ore mining process and iron ore mining equipments- Gulin. Introduction iron ore mining process flow including iron ore …
اقرأ أكثر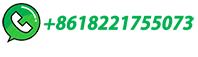
wet iron ore processing
Characterization and Beneficiation of Dry Iron Ore Processing … Iron ore is the basic raw material for iron and steel making. India is among the leading producers of iron ore in the world and produces about 150 million tons per annum (U. S. []).The total reserves of iron ore in India is around 28.5 billion tons, of this hematite ore is ...
اقرأ أكثر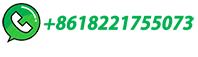
Iron Ore Beneficiation
The STET dry electrostatic fine iron ore separation process offers many advantages over traditional wet processing methods, such as magnetics or flotation, including: No water consumption. The elimination of water also eliminates pumping, thickening, and drying, as well as any costs and risks associated with water treatment and disposal.
اقرأ أكثر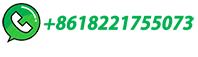
Magnetic Separator/ Wet Magnetic Separation Process/ Iron Ore …
Magnetic Separator Working Video. Introduction of Magnetic Separator: Magnetic separator is the professional refinement and iron removal equipment that can be used in the magnetic iron ore the dressing process such as magnetite, hematite, magnetic pyrite and limonite and non-metallic materials iron removal working including coal, quartz and gypsum.. The magnetic …
اقرأ أكثر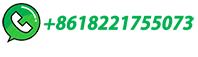
Safe carriage of Iron ore & other iron concentrates in bulk
the iron ore standard sampling procedure given in the IMSBC Code should be followed. Precautions for carriage of iron ore: Iron concentrates concentrates of iron are produced by either: the dry method, in which high grade ore is crushed to remove waste material, leaving a low moisture content in the powdered ore.
اقرأ أكثر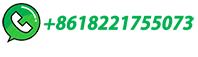
Wet High Intensity Magnetic Separators | Multotec
Wet High Intensity Magnetic Separators (WHIMS) from Multotec apply magnetism, matrix rotation and gravity to achieve para-magnetic materials separation. Applications include heavy minerals, ilmenite, manganese and iron ore (haematite) beneficiation; PGM upgrading as well as manganese recovery from slimes dams.
اقرأ أكثر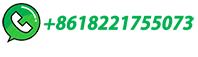
wet drum magnetic separator
Wet drum magnetic separator is a highly versatile magnetic separation equipment that separates and purifies various magnetic materials.It is mainly capable of effectively separating and recycling magnetic materials from slurry or wet materials. Wet drum magnetic separators are widely used in separating strong magnetic minerals, and can usually be easily integrated into existing mineral ...
اقرأ أكثر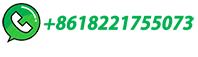