Ball-Milling Preparation of the Drug–Drug Solid Form of …
Stainless-steel bowls of 20 mL containing 10 stainless-steel balls (10 mm diameter) were used. In the case of the solid form (1:1), the ball-milling times were extended up to 150 min. Samples were periodically withdrawn to be able to characterize them (XRPD and DSC-TGA) at different milling times (30, 60, 90, 120, and 150 min).
اقرأ أكثر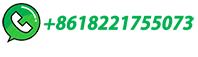
Effect of ball-milling time on microstructures and mechanical
The ball-milling time is the main parameter in low-speed ball-milling, which affects not only the reinforcement distribution but also the shape and size of the primary grains.
اقرأ أكثر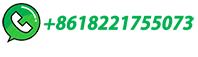
Transformation of quinoa seeds to nanoscale flour by ball milling
Among various size reduction techniques, high-energy ball milling is one of the most attractive means for plant-based foods. The objectives of the work were to investigate the influence of ball diameters (3, 6, and 13 mm) and milling time (2, 4, and 6 h) on particle size and microstructural properties of quinoa flours.
اقرأ أكثر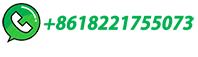
Ball milling alters the extractability and colloidal state of oat
Among various size reduction techniques, high-energy ball milling is one of the most attractive means for plant-based foods. The objectives of the work were to investigate the influence of ball diameters (3, 6, and 13 mm) and milling time (2, 4, and 6 h) on particle size and microstructural properties of quinoa flours.
اقرأ أكثر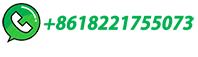
Ball vs. Jet Milling: Dry Techniques Explained
Energy Consumption – Jet milling tends to consume more energy than ball milling, especially when using steam, but it compensates with its ability to reach ultra-fine particles in a shorter time frame. Cost – Ball milling is generally more cost-effective for medium-coarse milling, while jet milling, though more expensive, delivers precision ...
اقرأ أكثر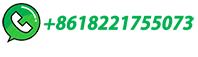
Powder Ball Milling: An energy balance approach to …
for grinding purposes. Ball milling is a development of the mortar and pestle, which was created in the Stone Age and has mostly not changed over time. It is extensively used for manufacturing cement, paints, pyrotechnics, ceramics. More recently, ball milling has assisted the progress of ultra-fine and nano-sized
اقرأ أكثر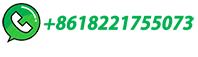
Effects of Mechanical Ball Milling Time on the …
During milling, to achieve the optimization of milled powders, several milling parameters need to be adjusted, such as the ball-to-powder weight ratio, milling speed, and milling time. Milling time is a key parameter, and it directly affects the morphology and distribution of the milled powders.
اقرأ أكثر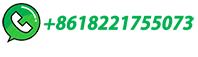
Long-time low-impact ball milling of multi-wall carbon nanotubes
In Fig. 3. we present the mean nanotube length as a function of milling time.The length decreased from over 2 μm to approx. 950 nm in the first 2 h of the milling, then the rate of change became lower and quasi linear.We could achieve mean lengths of 500, 200 and 140 nm after 120, 170 and 200 h of grinding, respectively.The whole MWCNT mean length vs. time in …
اقرأ أكثر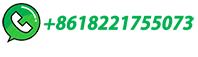
Research progress on synthesis mechanism and performance …
In recent years, the use of ball milling to synthesize biochar-iron based materials has become an emerging and promising method due to its low cost, environmental …
اقرأ أكثر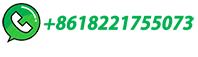
Ball milling coupled cascade magnetic separation to recover …
The effects of different ball milling time (10, 20, 30 and 40 minutes), ball milling rotating speed (300, 450, 600 and 750 rpm) and ball/powder mass ratio (5:1, 10:1, 15:1 and 20:1) were studied. Briefly, 5 g alkali disaggregation residues were added to each ball mill tank, and two tanks were used at the same time, so a total of 10 g alkali ...
اقرأ أكثر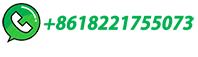
Effect of ball mill time and wet pre-milling on the …
The ball milling time of 2 h showed a positive effect on the hardness of the composites up to 100 . Thermal analysis results showed that the increasing zinc reinforcement ratio was increased thermal stability of the composite powders. The assessment of wear resistance was conducted using a block-on-ring tribometer, and the results ...
اقرأ أكثر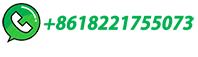
Effects of ball milling time on the synthesis and consolidation of
The effects of ball milling time on the synthesis and consolidation of WC–10 wt%Co powder were investigated by high energy milling in a horizontal ball mill.Nanostructured powder was mechanically alloyed after 60 min cyclic milling with a WC average domain size of 21 nm.The number of nanosize (<0.2 μm) particles increased with milling time.. …
اقرأ أكثر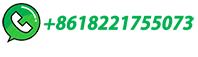
Exploring ball milling theory: A comprehensive guide
Ball milling is a fundamental and widely utilized technique in material processing. Understanding the principles behind ball milling theory is crucial for achieving optimal milling outcomes and …
اقرأ أكثر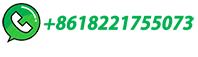
Effect of ball milling time and reaction solution …
The data reveals that when the water-cement ratio is set at 0.85, CS content at 30%, and CS ball milling time at 1 h, the resulting grouting material exhibits a fluidity of 279 mm, a water separation ratio of 3.13%, and achieves a strength of 15.6 MPa at 28 days. It boasts a stable and easily transportable slurry, which possesses a certain ...
اقرأ أكثر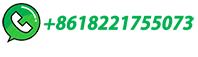
Effect of ball milling time on the thermoelectric properties of p-type
P-type (Bi,Sb) 2 Te 3 compounds were fabricated with high energy ball-milled powder and their thermoelectric properties were investigated as a function of the ball milling time. The fine grain sizes were confirmed with the X-ray analysis and the microscopy images in the samples fabricated with powders from long ball milling time. The values of the lattice …
اقرأ أكثر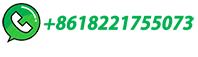
Effect of ball milling time on thermoelectric properties of …
The nanomaterial was prepared by varying the ball milling time and followed by hot press sintering. The crystal structure and phase formation were verified by X-ray diffraction and Raman Spectroscopy.
اقرأ أكثر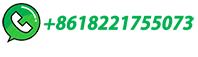
Effect of ball-milling time on microstructures and …
The ball-milling time is the main parameter in low-speed ball-milling, which affects not only the reinforcement distribution but also the shape and size of the primary grains. Therefore, in this study, to further optimise the process of low-speed ball-milling, the effects of ball-milling time on the microstructure, mechanical properties, and ...
اقرأ أكثر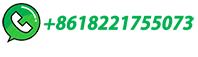
Effect of ball milling time on the formation and thermal
The broadening of particle size distribution observed with longer ball milling times is a common occurrence in high-energy ball milling processes . Zhang et al. [ 50 ] observed a decrease in average particle size when the milling time increased from 0 to 10 h, but an abnormal increase in size and the presence of numerous pores occurred when the ...
اقرأ أكثر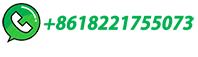
Ball milling of pyrolytic residue from oil sands with MnO
(a) Residual TPH content, and (b) Leachate TOC concentration in different materials. Experimental conditions: pyrolysis temperature = 500 ℃, retention time = 1 h, ball milling time = 1 h, ball milling speed = 500 rpm, ball/material ratio …
اقرأ أكثر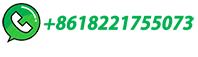
Effect of Ball Milling Time on the Microstructure and …
Different ball milling times (2 h, 4 h, 6 h, 8 h, 10 h, and 12 h) were employed as pretreatment for the powder, aiming to determine the optimal powder milling time. Following this, the preprocessed powder was subjected to discharge plasma sintering to fabricate high-silicon–aluminum composites. This study aims to examine the effects of ball ...
اقرأ أكثر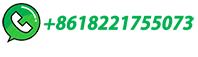
The Effect of Ball Milling Time on the Isolation of Lignin …
prolonging ball milling time from 3 to 7h obviously increased the isolation yields of MWL in bamboo residues (from 39.2% to 53.9%) and poplar sawdust (from 15.5% to 35.6%), while only a slight increase was found for the MWL yield of larch sawdust (from 23.4% to 25.8%). Importantly, the lignin substructure of ß-O-4 in the MWL samples from
اقرأ أكثر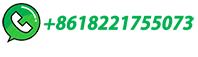
The Influence of Ball Milling Time and Sintering …
We systematically investigated the effects of different ball milling times (10 h, 20 h, 30 h, 40 h, 50 h) and sintering temperatures (700°C, 800°C, 900°C, 1000°C, 1100°C) on the structure and ...
اقرأ أكثر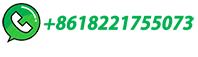
Exploring ball milling theory: A comprehensive guide
Ball milling is a mechanical process that involves the rotation of a drum containing grinding media, typically steel balls, at a high speed. The materials to be milled are loaded into the drum, and as the drum rotates, the grinding media collide with the materials, causing them to break down and reduce in size. ...
اقرأ أكثر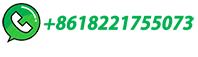
The Key Role of Ball Milling Time in the Microstructure and
Ni-5 vol.% TiC NP composites with ball milling times ranging from 8 to 72 h were prepared successfully by a powder metallurgy route. SEM-EBSD, XRD, TEM, the Vickers …
اقرأ أكثر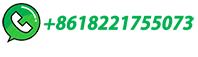
Effect of ball and feed particle size distribution on the milling
Fig. 5 shows the variation of size class 1 (M1) with the milling time for the two feed size distributions. For this coarser feed the 50 + 20+10 mm ball diameter mix breaks the material at a faster rate compared to the other ball matches. The availability of a ball size for a particular feed size ensures breakage occurs at a faster rate.
اقرأ أكثر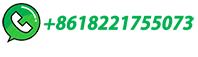
Influences of ball-milling time on gas-sensing
Thick-film devices using ball-milled composites were measured for electrical resistances in dry air (R a) in the temperature range 250–500 °C.As shown in Fig. 1, R a tended to increase with elongating ball-milling (BM) time but remained within the range of reliable measurement (about 10 8 Ω and bellow), which the electric resistance for all the devices was …
اقرأ أكثر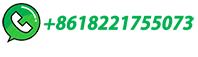
Wet ball milling activated oyster shells for multifunctional …
The results showed that when the ball milling time was 3 h, the ball-to-powder mass ratio was 10:1, and the solid–liquid ratio was 6:4, the activated AOS 7 exhibited the highest levels of suspended solid (Fig. S1 a) and water-soluble Ca ion (Fig. S1 b). The water-soluble Ca ion content was 22 times greater than that of the OS ball milled ...
اقرأ أكثر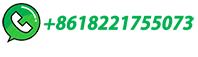
Effect of mechanochemical activation parameters on …
Also, the effect of ball size, milling time, and speed on the recovery efficiency of vanadium from vanadium-bearing steel slag (VBSS) was investigated. The VBSS powder was Na 2 CO 3 (aq)-milled with balls of varying size at different milling speeds and ignition/milling times. A mechanochemical activation leaching experiment was carried out for ...
اقرأ أكثر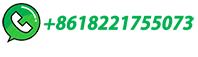
Effect of ball milling time on microstructure and mechanical …
The results revealed that there was an optimal ball milling time of 8 h existed for obtaining GNPs with uniform dispersion and an acceptable degree of defects. The Raman results indicated that the defects increased and the number of GNPs layers decreased with the increasing ball milling time.
اقرأ أكثر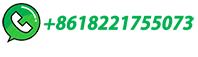
Effect of Ball Milling Time on the Performance of …
With the increase of ball milling time, D10, D50, D90, and DAV change to different degrees. As the ball milling time increases, D10 decreases from 13.9 to 10.2 µm. At a ball milling time of 50 min, D10 reaches a minimum value of 10.2 µm, a decrease of 26% than the D10 PBG without ball-milling treatment.
اقرأ أكثر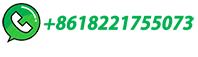