Ball Mill Design/Power Calculation
The basic parameters used in ball mill design (power calculations), rod mill or any tumbling mill sizing are; material to be ground, characteristics, Bond Work Index, bulk density, specific density, desired mill …
اقرأ أكثر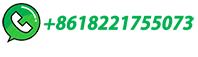
Characterization and comparison of gray cast iron powder …
The cast iron scrap investigated in this study was pearlitic lamellar gray cast iron (Fig. 1) obtained during the dry machining of slabs used for making car engine components.The chemical composition of this material is reported in Table 1.The size of the scraps used was in the range − 12 + 30 mesh.Planetary ball milling and target jet grinding were used to pulverize …
اقرأ أكثر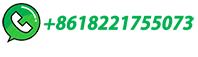
Recent Advances in Ball-Milled Materials and Their …
Ball milling, as a cost-effective and eco-friendly approach, has been popular in materials synthesis to solve problems involving toxic reagents, high temperatures, or high pressure, which has the potential for large-scale …
اقرأ أكثر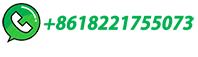
Interface behavior and oxidation consolidation mechanism of titanium
The experiments mainly include the pretreatment of titanium-bearing iron sand by ball-milling and the preparation and oxidation-roasting of titanium-bearing iron sand pellet. The detailed steps are shown in the Fig. 3. Firstly, the titanium-bearing iron sand was pretreated in the ball-milling machine with a mass ratio of ball to material of 1:3.
اقرأ أكثر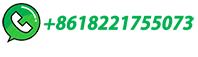
Enhanced Cr (VI) removal of zero-valent iron with high proton
In this study, we prepared oxalated zero-valent iron (OX-ZVI) by mechanically ball-milling ZVI and oxalic acid dihydrate to replace iron oxide shell with FeC 2 O 4 ·2H 2 O shell, aiming to check how proton diffusion among the ZVI shell affect the surface-bound Fe 2+ generation and the Cr(VI) removal ability. The resulted samples were characterized by …
اقرأ أكثر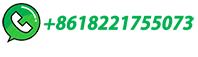
Ball Milling Method for Synthesis of Nanomaterials
For all nanocrystalline materials prepared by high-energy ball milling synthesis route, surface and interface contamination is a major concern. In particular, mechanical attributed contamination by the milling tools (Fe or WC) as well as ambient gas (trace impurities such as O 2, N 2 in rare gases) can be problems for high-energy ball milling ...
اقرأ أكثر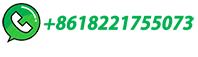
Effect of ball milling energy and carbon content on …
However, it has a wide bandgap of 5.96 eV owing to the strong coupling between iron and fluorine, which results in a low electrical conductivity [14, 15]. ... Ball milling of carbon combinations is a simple and effective method that can simultaneously perform particle grinding and mixing. It is classified into low-energy and high-energy ball ...
اقرأ أكثر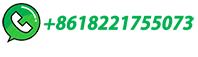
(PDF) Research progress on synthesis mechanism …
In recent years, the use of ball milling to synthesize biochar-iron based materials has become an emerging and promising method due to its low cost, environmental friendliness, and...
اقرأ أكثر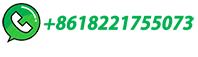
Silicon nanoparticles synthesised through reactive high …
inevitable milling contaminants, such as iron from the steel milling media, are introduced into the product during the ball milling process.[17,18] In this paper, we have synthesised SiNPs through RHEBM in the presence of 1-hexene. The iron impurities were removed from the ball milling product by both physical (GPC separation) and chemical methods
اقرأ أكثر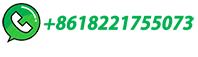
Mesoporous ball-milling iron-loaded biochar for enhanced sorption …
Positive surface charge and large surface area were responsible for the outstanding removal performance of RR120 by ball-milling Fe-biochar composite: (1) The adscititious Fe would be converted to β-FeOOH during pyrolysis, which significantly improved the zeta potential of biochar and thus facilitated the electrostatic adsorption for RR120 ...
اقرأ أكثر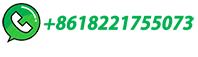
Remediation of Cr(VI)-contaminated soil by ball milling …
Ball milling modification could promote iron dispersibility and electrical conductivity, increase oxygen-containing functional groups and enhance electron release and transfer [9]. Our previous study showed that ball-milled zero-valent iron biochar composites (BM-ZVI/BC) could efficiently remove Cr(VI) from water bodies with a maximum Langmuir ...
اقرأ أكثر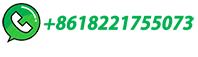
Simulation of wet ball milling of iron ore at Carajas, Brazil
The tests were made in a steel cylindrical ball mill of 250 mm internal diameter (D T) and 250 mm length ... What was expected to be a straightforward application of known techniques to construct a mill simulator applicable to ball milling of iron ore has shown a number of unanticipated problems.
اقرأ أكثر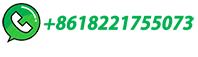
Research progress on synthesis mechanism and performance …
In recent years, the use of ball milling to synthesize biochar-iron based materials has become an emerging and promising method due to its low cost, environmental friendliness, and potential for ...
اقرأ أكثر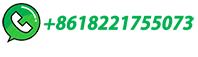
Ball milling of pyrite in air to significantly promote the …
Natural pyrite (FeS 2) has been widely used as heterogenous Fenton catalyst due to the unique iron supplying and ferrous regeneration performance, however, natural pyrite has poor catalytic activity due to the low surface reactivity.Ball milling is commonly used to modify pyrite, but the mechanism has not been thoroughly studied. In our work, by optimizing the ball milling …
اقرأ أكثر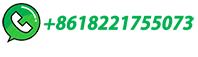
Structure and properties of Fe-N-C composites obtained by …
Bulk nanocrystalline composites produced by high-energy ball milling of nitrated iron powders followed by dynamic pressing are studied. Composites consist of three phases α-Fe + γ′-Fe4N + Φ, where the nature of the Φ phase is determined by the milling environment (nitrogen, heptane, or xylene). The microhardness of composites is 6–7 GPa at a density of …
اقرأ أكثر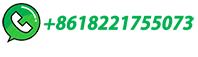
Ball-milled zero-valent iron with formic acid for effectively …
The addition of FA to ball-milling could dramatically enhance the performance of ball-milled ZVI (ZVI bm) towards Cu(II)-EDTA removal and increase the removal rate constant by 80 times. This conspicuous improvement of Cu(II)-EDTA elimination was attributed to the ferrous formate (Fe(HCOO) 2 ) shell formed on the surface of FA-ZVI bm .
اقرأ أكثر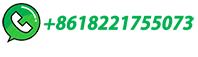
Enhanced breakage of the aggregates of nanoscale zero-valent iron …
Aggregates of nanoscale zero-valent iron (nZVI) are commonly encountered for nZVI in aqueous solution, particularly during large-scale nZVI applications where nZVI is often in a highly concentrated slurry, and such aggregates lower nZVI mobility during its in-situ remediation applications. Herein, we report that the ball milling is an effective tool to break the nZVI …
اقرأ أكثر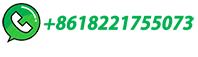
Investigation of nano Iron Carbide production by ball milling
In this study, two routes were used in order to produce iron carbide. Graphite powders were amorphisized and reduced to nano-size by ball milling process for C source.
اقرأ أكثر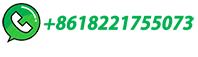
Research progress on synthesis mechanism and performance …
In recent years, the use of ball milling to synthesize biochar-iron based materials has become an emerging and promising method due to its low cost, environmental friendliness, and potential...
اقرأ أكثر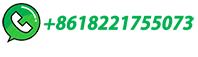
New insights into ball-milled zero-valent iron
Ball milling is an effective and economical method, which has an important application prospect in overcoming the passivation problem of zero-valent iron (ZVI) and …
اقرأ أكثر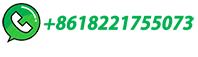
STEEL MILLING BALLS FOR BALL MILLS Specifications
This standard is applied to milling balls with diameter of 15-120 mm made of low alloy carbon steelor alloy carbon steel using methods of cogging, beating out and pressing and used for milling of iron stone, coal, cement and other materials in ball mills. 2. …
اقرأ أكثر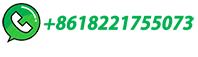
Ball milling sulfur-doped nano zero-valent iron @biochar …
The regeneration experiments of composites showed that re-ball milling destroyed the surface iron oxide layer to improve the properties of the recovered material. This is an essential step in the design of P-removal agents to implement anti-aging and commercialization of adsorbents for engineering applications.
اقرأ أكثر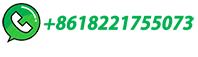
Enhanced breakage of the aggregates of nanoscale zero-valent iron …
Experiments are first conducted to compare the breakage of the nanoparticle aggregates via ball milling (bead velocity: 8.9 m/s, bead diameter: 0.4 mm, chamber porosity: 45 %), mechanical mixing (3500 rpm and 500 rpm) with and without ultrasonication (40 W) (Fig. 1).The aggregates before and after the breakage are characterized using two sizing methods, …
اقرأ أكثر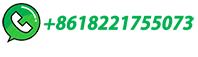
Effect of Ball-Milling on the Oxygen Reduction …
Ball-milling rates from 100 to 800 rpm were investigated with 400 rpm proving to be the optimum value. The effect of 1,10-phenanthroline-to-iron ratio in the precursor mixture was also studied, with a 12/1 molar ratio leading …
اقرأ أكثر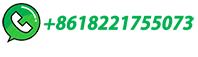
Effective removal of Cr(VI) from water by ball milling sulfur …
In addition, the ball milling is capable of producing a substantial amount of S-mZVI, catering to the demands of industrial-scale production. Nevertheless, few studies have investigated the remediation of Cr(VI) by ball milling sulfur-modified micron zero-valent iron (S-mZVI bm). Hence, it is essential to prepare sulfur modified mZVI by ball ...
اقرأ أكثر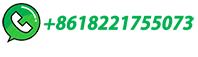
Microwave Absorption Properties of Flaky Carbonyl Iron @ Fe
In this work, large-diameter flaky carbonyl iron (FCI) and FCI@Fe3O4 composite materials were prepared by employing a simple plasma-assisted ball milling and heat treatment process. Large FCI was obtained, with 30-70 μm diameters and a thickness of 300 nm. The results show that, compared with the original polycrystalline carbonyl iron fiber, FCI exhibited …
اقرأ أكثر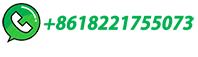
Enhanced Cr(Ⅵ) reduction by zero-valent iron and ferroferric …
The Fe 0-Fe 3 O 4 composites were prepared by a planetary ball milling machine in a zirconia tank (500 mL) and zirconia balls (Beijing Grinder Instrument Co Ltd, China). The basic parameters of ball milling and material ratios were referred to previous research and adjusted under the actual experimental conditions [[6], [17]].
اقرأ أكثر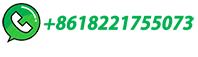
Navigating Ball Mill Specifications for Theory-to-Practice
Therefore, each ball mill model will feature a different energy profile dependent on its planetary disk and jar dimensions, irrespective of the chosen milling conditions (rpm, …
اقرأ أكثر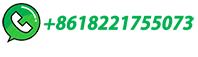
Efficient recovery of electrode materials from lithium iron …
Efficient separation of small-particle-size mixed electrode materials, which are crushed products obtained from the entire lithium iron phosphate battery, has always been challenging. Thus, a new method for recovering lithium iron phosphate battery electrode materials by heat treatment, ball milling, and flotation was proposed in this study. The difference …
اقرأ أكثر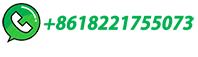
Direct Mechanocatalysis: Using Milling Balls as …
We propose to combine the symbol for mechanochemical reactions introduced by Hanusa in addition with the catalytic element inside the milling balls as a symbol for direct mechanocatalysis.
اقرأ أكثر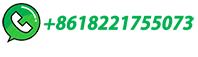