THE PERFECT SINTER PLANT SOLUTIONS FOR FULLY …
As a leading supplier of complete sinter plants, Primetals Technologies provides engineering, design, and equipment as well as integrated automation solutions. Specific technology …
اقرأ أكثر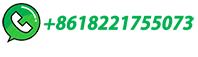
Adapting to Raw Materials Challenges: Part 1 – …
In Part 1, we will look at how the chemistry of the iron oxide pellets affects the use of DRI/HBI in the EAF and the BF. We will explore what makes a pellet DR-grade and compare it with a BF-grade pellet, and discuss the advantages and …
اقرأ أكثر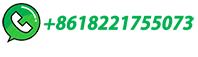
FUNCTIONS OF VARIOUS DEPARTMENTS OF RINL/VSP
Functions & Duties The functions and duties of the employees of the Company stems mainly from the provision of the Companies Act, 1956 and Memorandum & Articles ... Sinter Plant Sinter is a hard & porous ferrous material obtained by agglomeration of Iron Ore fines, Coke breeze, Lime Stone fines, Metallurgical wastes viz. Flue dust, mill scale ...
اقرأ أكثر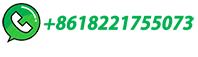
THE PERFECT SINTER PLANT SOLUTIONS FOR FULLY …
to bring your sinter plant in line with the latest technologies. Our lifecycle management spans the entire service life of the sinter plant, offering much more than just after-sales service. • Extensive experience in the sintering process – building and modernizing sinter plants for over 5 decades • Efficient project execution –
اقرأ أكثر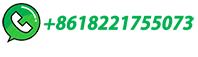
Theory and Practice of Sintering of Iron ore – IspatGuru
Sinter presents better softening and melting behaviour than pellets or ore, but worse meltdown and high temperature gas resistance. It has been seen that a mixed burden containing 65 % sinter, 20 % lump ore, and 15 % pellets is slightly better than other compositions in terms of FT and ST, meltdown and high temperature gas resistance.
اقرأ أكثر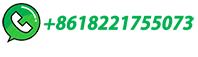
(PDF) Fabrication of Sintered Annular Fuel Pellet for …
Finally, thermal conductivity as a function of temperature has revealed that sintered ThO2-SiC composites showed an increase of up to 56% in thermal conductivity compared to pristine ThO2 pellets ...
اقرأ أكثر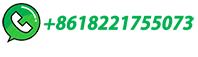
Recycling pre-oxidized chromite fines in the oxidative sintered pellet
Sintered pellets are then cooled by air blown through the pellet bed from below. Thereafter, the sintered pellets are discharged and screened to remove < 6 mm material, but screening at a smaller aperture has also been observed by the authors during plant visits at FeCr producers applying this process.
اقرأ أكثر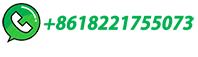
Why does the color of the pellet get changed after sintering?
I have sintered pellets of Ce-doped SrTiO3 at 1400 degree Celcius for 24 hrs. the color of green pellet was light-orange but the sintered pellet is black in color. ... As a function of calcination ...
اقرأ أكثر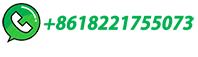
Sintered pellets: A simple and cost effective method to predict …
The pellets were then sintered twice in an air atmosphere in a tube furnace at 1500 °C for 10 h each time in an air atmosphere. The color of the pellets changed from white to yellow after sintering, as shown in Fig. 1, indicating that a reaction has occurred. Download: Download full-size image; Fig. 1.
اقرأ أكثر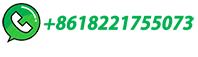
Design And Fabrication Of Iron Ore Sintering Machine | PDF
7. Amount and quaility of solid fuel in the charge. 8. Nature of ore fines. E.g. chemical composition. 9. Non-uniformity in the bed composition. 3.3 Role of Sinter Plant The function of the Sinter Plant is to supply the blast furnaces with sinter, combination of blended ores, fluxes and coke, which is partially 'cooked' or sintered.
اقرأ أكثر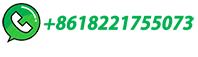
Mechanisms in oxidation and sintering of magnetite iron ore green pellets
Thermal volume changes and oxidation mechanisms in magnetite iron ore green pellets balled with 0.5% bentonite binder, as a function of raw material fineness and pellet porosity, are shown. When a pellet starts to oxidize, a shell of hematite is formed around the pellet while the core still is magnetite.
اقرأ أكثر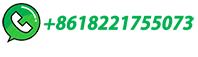
Iron Ore – Beneficiation & Pelletization Division
CPT plant functions on a circular design with a low building profile and small overall footprint. It was developed by Primetals Technologies Austria , a joint venture of Siemens AG and Mitsubishi. ... Sinter and Pellet plant. Provision is also made to feed directly 0-20 mm raw material as plant feed.
اقرأ أكثر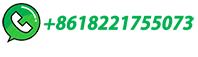
SINTER PLANT WASTE HEAT RECOVERY PROCESS AND …
An important function of the sinter plant is to utilized waste iron-bearing materials to the blast furnace to produce iron. Sintering machine agglomerates fine ores to make sinter that supplied to Blast furnace of integrated steel plant. Sinter cooler cools down the red hot sinter from the sintering machine by cooling air. ...
اقرأ أكثر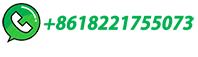
Construction of Fukuyama No. 3 Sinter Plant and …
Sinter Plant. The new plant was constructed on the site of the former No. 3 Sinter Plant, which was in opera-tion until 1982. Construction began after first removing the remaining equipment of the former No. 3 Sinter Plant (proportional bin, drum mixer, sinter plant build-ing, screen building, electrostatic precipitator, main
اقرأ أكثر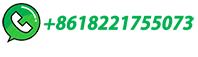
Fabrication of UO 2 -Gd 2 O 3 Fuel Pellets
2) Low sintered density and bloating were noticed in some lots of sintered pellets. Both the problems were traced to the second supply of the powder. While the powder from "A" was crystalline and flowed freely, that from "B" was less crystalline, had a greater BET specific surface area, had higher moisture content, was nonflowable and ...
اقرأ أكثر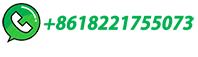
Sinter Plant Design, Engineering, Construction
A Sinter plant in a steel plant is the final operation in a series of measures to prepare iron ore for blast furnace smelting.A sinter plant is an enterprise with a complicated technological process for producing the final product – …
اقرأ أكثر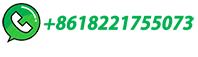
The Functional Resonance Analysis Method for a systemic …
The pellet and the sinter plants are two different types of iron ore's preparation plants for the BF's burden. Pellets are generally made from one well-defined iron ore or concentrate at the mine and are transported in this form. ... Technical function provided by plant databases: Plan sinter target quality: Establish the target quality of the ...
اقرأ أكثر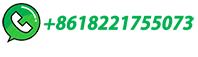
FUNDAMENTALS OF IRON ORE, SINTER FEED AND …
sinter and pellet feed, which are exported and/or processed locally. Unfortunately, because of these material's flow behavior during heavy rainy seasons, instances of handling problems occur. Iron ore, whether coarse or fine, dry or wet, sinter feed and pellet feed tend to plug in chutes, stick on conveyors, and cake in stockpiles and silos.
اقرأ أكثر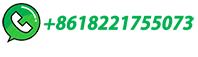
sintered pellets produced with UG2 or metallurgical …
previously sintered pellets. The green pellets are then ignited in a furnace, and air is passed through the pellet bed to sinter the pellets. The amount of carbon present in the green pellets is limited to supply just enough exothermic energy to sinter the pellets properly (Beukes et al., 2010). The oxidative sintered pelletized feed technology is
اقرأ أكثر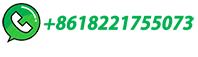
Sintering and Pelletizing
Traveling grate pelletizing plant is an induration technology for iron ore pellet production for a wide range of plant capacities. Traveling grate sinter plant reduces off-gas volumes and the emission of hazardous pollutants, while …
اقرأ أكثر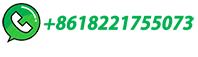
Study of Liquid Phase Formation during the Sintering of …
a binder. The physical and metallurgical properties of the sintered pellets depend on the formation of liquid phase. The properties sintered pellets samples collected from the sintering plant were evaluated in the laboratory. The compressive strength of the samples varied significantly from 5 kg/pellet to 305 kg/pellet. The microstructure of ...
اقرأ أكثر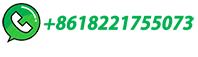
Sintering plant at a glance | PPT
10. 10 STOCK BINS AND PROPORTIONING SECTION A. TO STOCK RAW MATERIALS : There are three similar series of over head bunker and conveyors to feed three sinter machines at a time. Each series contains 23 bunkers . Materials are stored in the bunkers in following order : BUNKER No. TOTAL BUNKER MATERIAL 1 – 6 06 Iron ore fines 7 – 13 …
اقرأ أكثر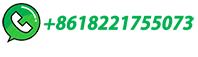
Iron Ore Pelletizing Process: An Overview | IntechOpen
Viscosity as a function of pH and temperature, adsorption: Drop number, strength (green, dry), thermal shock (550–600°C) ... and superior environmental performance of pellet plants as compared to sinter plants; the main iron producing systems, blast furnace, and DR reactors, will not be replaced in the near future. Advertisement ...
اقرأ أكثر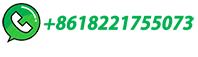
Use of Artificial Neural Network to Predict the Yield of Sinter Plant
The main feeds for Blast Furnace are Sinters and Pellets. In the first part of twentieth century, Sinter making technology is evolved to treat and utilize the fines generated during mining of iron ore as well as during steel making process in a better way. ... Use of Artificial Neural Network to Predict the Yield of Sinter Plant as a Function ...
اقرأ أكثر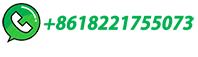
Sinter Plant
Sinter plants are the major contributor to dust emissions from integrated ironworks and steelworks. The dust emissions from sinter plants are generated from raw material handling, …
اقرأ أكثر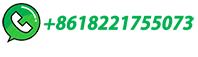
USE OF SINTERED PELLETS IN PRODUCTION OF HIGH …
After cooling, the sintered pellets are screened on a rotary screen and the under sized pellets below 6 mm are recycled to the grinding mill. Sintered pellets of +6 mm size are tran sported and stored in a shed for smelt-ing trials. The chemical composition of sintered pellets and their crushing strength is given in Table-2. 4.
اقرأ أكثر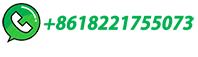
Investigation of the Contents of the Stack Emissions of Iron Ore Sinter
Introduction. The stack emissions of the iron ore sinter plant contain flue gas with CO, CO 2, H 2 O vapors; fine particles of iron ore, sinter components; and particulates of SO x, NO x, KCl, and PCDD/Fs.The appearance of the stack emissions varies with the plume contract, its contents, and the meteorological conditions, especially sunlight intensity, scattering, time, …
اقرأ أكثر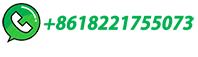
Characterization and Beneficiation of Dry Iron Ore …
Characterization and Beneficiation of Dry Iron Ore Processing Plant Reject Fines to Produce Sinter/Pellet Grade Iron Ore Concentrate P. Dixit1 & D. Makhija1 & A. K. Mukherjee1 & V. Singh1 & A. Bhatanagar2 & R. K. Rath3 Received: 6 September 2018 /Accepted: 12 September 2018 /Published online: 18 September 2018
اقرأ أكثر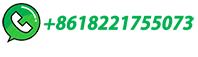
IMPLEMENTATION OF THE INTENSIVE MIXER AT …
ramp-up was characterized by gradual increases of pellet feed, burnt lime and moisture. It was used up to 25% of pellet coarse in charge of iron ore at sintering process. Key words: Sinter plant; Intensive mixer; Pellet feed. 1 Technical contribution to the 6th International Congress on the Science and Technology of
اقرأ أكثر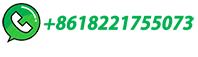
Pelletizing Process
Sintered ore is made by partially melting and sintering coarse iron ore 1 to 3mm in size into products having a size of 15 to 30mm. The sintering process uses the combustion heat of …
اقرأ أكثر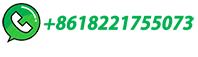