Dry beneficiation of iron ore
The haematite ore in South Africa is processed in a dry process to a HQ lump ore with 64 % iron content and a sintered fine ore with 63.5 % iron content. For fine ore beneficiation, wet processes are used. Capacity at the Minas Rio is to …
اقرأ أكثر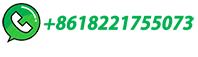
An iron ore-based catalyst for producing hydrogen and …
Ball milling of the iron ore at 300 rpm for varying times – from 30 to 330 min – was studied to determine the effect of milling time on methane conversion. ... High energy ball milling proved to be an effective method for optimising an iron ore catalyst for the methane pyrolysis process. Ball milling of the iron ore enabled up to a five ...
اقرأ أكثر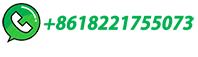
How to Recover Iron from Magnetite: 4 Methods and Stages
Magnetite is the main mineral in iron ore beneficiation, which has industrial value and is mined in large quantities. Here we will introduce the beneficiation method and process of magnetite ore in detail. What is magnetite? Magnetite is an iron oxide ore, which belongs to the equiaxed crystal system, and its chemical formula is Fe 3 O 4. The ...
اقرأ أكثر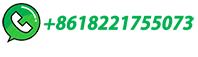
Mills for minerals and ores
Successful inauguration of the New Steel Pilot Plant with a LOESCHE Ore Grinding Plant (OGPmobile) in Ouro Preto, MG, Brazil. Ouro Preto – The company New Steel has developed a revolutionary new process for iron ore concentration for which New Steel has been awarded with the internationally highly esteemed Platts Global Metals Award for Innovation 2015.
اقرأ أكثر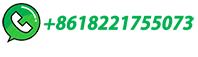
Eco-efficient and cost-effective process design for magnetite iron ore …
A detailed comparison of four circuit options for magnetite iron ore in terms of cost- and eco-efficiency. ... Assessment of different eco-efficient comminution process circuits to treat magnetite iron ore. ... AG milling in closed circuit with hydrocyclones and pebble crushing – rougher magnetic separation – ball milling – cleaner ...
اقرأ أكثر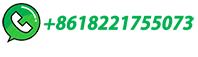
Mineral separation process of magnetic iron ore
Its core reduces mill feed size exactly, energy consumption with further reduction ore grinding, in the ore dressing energy consumption, because ore grinding accounts for 50%, this technology takes three grades to be broken for thick broken (300mm is following), in broken (200mm is following), the closed circuit flow process of thin broken (25mm is following) makes mill feed …
اقرأ أكثر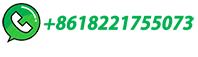
Understanding the Steel Making Process: A Flow …
The steel making process starts with the melting of iron ore in a blast furnace, where impurities are removed and carbon is added. Secondary steelmaking involves refining the composition by adding or removing elements …
اقرأ أكثر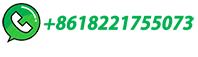
Samarco Iron Ore Mine, Alegria, Brazil
At 396km, this iron ore slurry pipeline is the world's longest and offers environmental safety and 99% average availability. The new slurry pipeline built in 2008 also measures 396km. ... The installation of the third pellet plant enabled Samarco to process nearly 24Mt/y of ore concentrate. It allowed Samarco to produce approximately 21.6Mt ...
اقرأ أكثر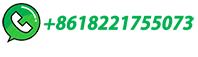
Evaluation of Quality Parameters and Mineralogy of Iron Ore …
The present article focuses on incorporating mill scale, a steel plant solid waste, into the iron ore pelletization process. The characterization results indicated that the mill scale contained about 71% of Fe and predominantly consists of magnetite and wustite mineral phases. A detailed pelletization study is conducted using the mill scale at different proportions (0%, …
اقرأ أكثر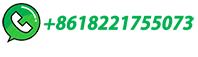
How to Process Iron Ore?
The process flow of iron ore is as follows: crushing, screening, grinding, beneficiation, drying, etc. ... Iron ore processing equipment 1. Ball mill. Ball mill plays an irreplaceable role in ...
اقرأ أكثر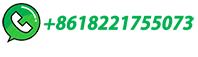
Iron Mining Process
The iron ore is separated from the taconite using magnetism. The remaining rock is waste material and is dumped into tailings basins. The taconite powder with the iron in it is called concentrate.
اقرأ أكثر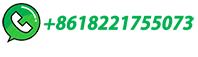
Iron Ore Mining Process: From Extraction to Export
Discover the iron ore mining process, from blasting to export, and its vital role in steel production. Learn about iron ore extraction and its history. Are environmental regulations, health and safety concerns or potential profit loss a concern right now? Request Free Quote +61 7 5667 8550. HOME;
اقرأ أكثر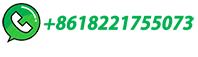
The Sintering Process of Iron Ore Fines – IspatGuru
The process of sintering is basically a pre-treatment process step during iron making for the production of the charge material called sinter for the blast furnace from iron ore fines and also from metallurgical wastes (collected …
اقرأ أكثر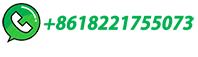
Tin Ore Processing
In the complex milling ore the tin is intermixed very closely with the sulphides, so that it becomes necessary to collect all the mineral present in order to obtain clean tailings. ... is the high working cost, due partly to the amount of manual labour required, and partly to the intermittency of the process. It is essential, in order to work ...
اقرأ أكثر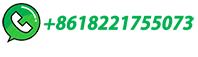
Recycling and Reuse of Iron Ore Pellet Fines | SpringerLink
For pelletization study, as received iron oxide pellet fines were ground to below 150 μ using ball mill. The particle size distribution of ground iron ore fines was determined by the Malvern particle size analyzer (Hydro 2000MU, UK) and shown in Fig. 2.Blaine number was measured to determine surface area of the iron oxide pellet fines using air permeability …
اقرأ أكثر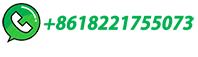
Optimization of the Iron Ore Direct Reduction Process …
Iron ore direct reduction is an attractive alternative steelmaking process in the context of greenhouse gas mitigation. To simulate the process and explore possible optimization, we developed a systemic, multiscale process model. The reduction of the iron ore pellets is described using a specific grain model, reflecting the transformations from hematite to iron. …
اقرأ أكثر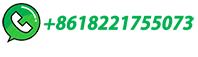
NRRI advances efficient grinding technology on the Iron Range
A crucial step in mineral processing – and in Minnesota's iron ore processing – is comminution, a process of crushing and grinding. Large rocks must first be crushed and …
اقرأ أكثر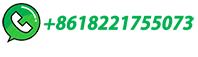
MINERAL PROCESSING
Suitable minerals such as copper or iron ore are listed in table 4. This type of mill has the distinct advantage of accepting coarse feedstock and supplying a relatively fine finished product, often ... of a milling process to provide a reduced size feedstock for a further milling process. Coke Products for the glass industry Cement clinker ...
اقرأ أكثر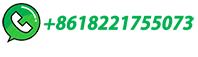
The six main steps of iron ore processing
Iron processing | Definition, History, Steps, Uses, & Facts
اقرأ أكثر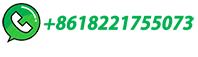
A novel process for highly efficient separation of boron and iron …
A facile route for simultaneous activation and separation of boron and iron from ludwigite ore at low temperature under the synergistic effect of microwave heating and sodium carbonate (Na 2 CO 3) was reported.It was shown that the composite system would absorb microwave energy well and promote the reduction of iron oxides and formation of water …
اقرأ أكثر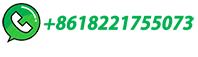
Processing of Magnetite Iron Ores
Although the majority of current steel production is supported by iron ore sourced from high-grade haematite deposits, the long-term growing demand for steel has led to higher raw material prices and opened the way for many new magnetite deposits to also be developed._x000D_ There is a rich and long history of magnetite ore processing in Western countries, including …
اقرأ أكثر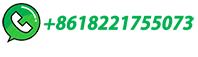
Iron Ore Mining Process: From Extraction to Export
Discover the iron ore mining process, from blasting to export, and its vital role in steel production. Learn about iron ore extraction and its history
اقرأ أكثر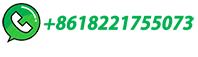
Iron Ore Beneficiation Process Flowsheet PDF
Iron ore beneficiation process flowsheet.pdf - Free download as PDF File (.pdf), Text File (.txt) or view presentation slides online. This document provides a flow diagram of a mineral processing plant. It shows the process flow from receiving the raw ore feed hopper through various crushing, grinding, and flotation circuits to produce concentrate products.
اقرأ أكثر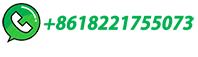
Development of a Novel Grinding Process to Iron Ore …
CAMPOS et al. (2019d) also showed using process simulations that operating with 40% of product edge recycle in an industrial-scale HPGR would allow achieving an increment in the BSA of the iron ...
اقرأ أكثر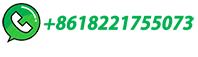
Pelletisation process | PPT
2. Introduction To Pelletisation Process Pellets are spherical balls formed by the agglomeration of natural or ground iron ore fines in the presence of moisture and binder These green balls of 5 – 20mm size are then dried, …
اقرأ أكثر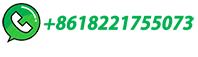
Low grade Iron Ore Beneficiation and the Process of Jigging
concentration, density, gangue material, gravity separation, iron ore beneficiation, Jig, Jigging, Low grade iron ore, Low grade Iron Ore Beneficiation and the Process of Jigging . Iron ore resources are getting consumed at an accelerated rate because of the growth in the production of iron and steel. Due to this reason the availability of high ...
اقرأ أكثر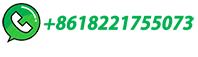
Iron Ore Smelting Process
The ore is loaded into a blast furnace along with measured quantities of coke and limestone. Hot combustion air is supplied to the furnace and some form of fuel used to raise the temperature. The iron is reduced from the ore by carbon in …
اقرأ أكثر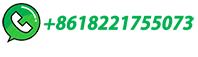
sbm/sbm iron ore milling flow.md at main · chengxinjia/sbm
Contribute to chengxinjia/sbm development by creating an account on GitHub.
اقرأ أكثر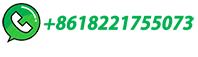
Iron Ore Milling Process
Iron Ore Milling Process. صفحه اصلی; Iron Ore Milling Process; IRON AND STEEL. A general flow diagram for the production of raw steel from iron ore is presented in Exhibit 2. In general, the process involves (1) beneficiation of the iron ore, (2) either direct-reduction or reduction in an iron blast furnace, (3) processing in ...
اقرأ أكثر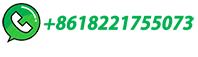
Magnesite Ore Processing: Separation and Calcination
Crush the raw ore to 10-0mm with a jaw crusher and a roll crusher. 2 Washing: Set a trommel screen to remove the muddy impurities in the ore. 3 Grinding: Use a ball mill to grind the raw ore to 95%-0.074mm. 4 Magnetic separation: Use a magnetic separator to remove iron impurities in the pulp. 5 Flotation:
اقرأ أكثر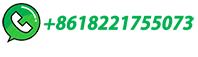