Of Proposal For 2.4 MTPA Pellet Plant Over an Area of …
Iron Ore Fines generated in the company's iron ore mines and nearby mines in Joda- Barbil area will be used to make iron ore pellets by agglomerating them. This product will be used for captive consumption in the company's sponge iron plants as well as will be sold in the open market. 1.2 Details of Products Proposed
اقرأ أكثر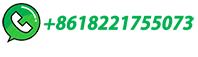
Pelletization Solutions
Pelletizing is the process of transforming iron ore fines into spherical pellets through agglomeration and induration to be used as feed to a blast furnace or direct reduction systems …
اقرأ أكثر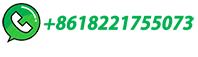
Sintering plant at a glance | PPT
•The granulometry of iron ore fines, used in sintering, has a great influence on sinter plant performance. •Laboratory Experiments were conducted with different granulometry of iron ore fines to assess its influence on sinter …
اقرأ أكثر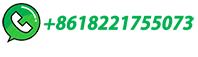
Tebinbulak 5 MTPY Iron Ore Pelletizing Plant
The pelletizing plant in the Tebinbulak project is part of a comprehensive mining and metallurgical complex. It will process ore into iron pellets, which are essential for producing direct reduced iron (DRI). This plant is designed to handle a substantial portion of the 3.6 million tons of DRI planned annually.
اقرأ أكثر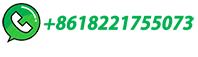
Fine Ore Direct Reduction Circored
of iron ore fines. The flexible process, which produces highly metalized direct reduced iron (DRI) or hot briquetted iron (HBI) that can be fed directly to an electric arc furnace, has proven ... Pelletizing plant Dust recycling H 2 plant Pig iron DRI / HBI DRI / HBI Iron ore Steel d 80 = 45 ƒm ~1.0 t CO 2 / t steel ~1.8 t CO 2 / t steel d 80 ...
اقرأ أكثر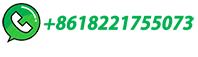
MINI-PELLETIZING: CRISIS AS AN OPPORTUNITY FOR INNOVATION …
PDF | Circular Mini-Pelletizing Plant was presented as an alternative process to recover and recycle iron ore fines of small mines and iron makers. | Find, read and cite all the research you need ...
اقرأ أكثر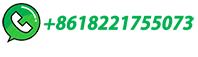
Optimization of Pellet Plant Straight Grate Induration …
Indian iron ores are suffering from high amounts of alumina and loss on ignition (LOI), which are deleterious constituents in both the pelletizing as well as iron making processes. Iron ore fines utilized in pellet making consist of alumina in the range of 3.20–3.35% and LOI in the range of 3.50–3.70%. Detailed palletization studies have been carried out on …
اقرأ أكثر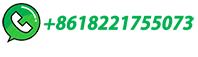
Lloyd Metals 4 MPTY Iron Ore Pelletizing Plant
Lloyd Metals is undertaking a significant project to establish a 4 MTPY Iron Ore Pelletizing Plant in India. This initiative is pivotal in supporting the country's steel industry by converting iron ore fines into high-quality pellets.
اقرأ أكثر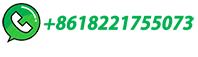
Iron Ore Pelletization: A Critical Review of Processes and
Pelletization involves converting iron ore fines into compact pellets, which are then used in blast furnaces or direct reduction iron processes, contributing to more sustainable and efficient steel …
اقرأ أكثر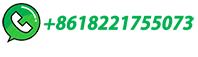
Hazard Identification, Risk Assessment, and Control …
The pellet plant used travelling grate technology to convert low grade fines into value-added pellets. The slurry was received at the pellet plant from the beneficiation
اقرأ أكثر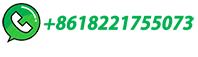
Iron Ore Pelletizing Essential in Meeting Future …
Iron ore pelletizing, or balling, is the process of transforming fines into spherical granules anywhere from 8 – 16mm in size via tumble-growth (agitation) agglomeration using either a disc pelletizer (pan granulator) or rotary drum.
اقرأ أكثر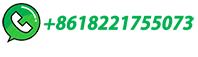
Pelletization of iron ores and the type of wear liners used in …
4. Need of pelletizing of Iron ores Configuration of Iron ore fines as tightly packed structure that restricts heat and air flow in blast furnace. Utilization of iron ore fines of size even 0.5-0.15mm. Extending the life of iron ore reserves of nation. To improve Blast furnace performance Increase in blast furnace productivity. Decrease in uses of blast furnace fuel/coke …
اقرأ أكثر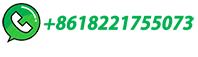
Usage of High-LOI Iron Ore Fines in Pellet Making
From laboratory studies, it has been found that for utilization of e high-LOI iron ore fines (7–9%) in pellet making to achieve desired pellet properties, induration firing cycle should be ...
اقرأ أكثر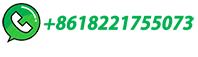
COMPARISON OF SINTER AND PELLET USAGE IN AN INTEGRATED STEEL PLANT 1
For indurated pellets, carboxymethyl cellulose (210.2 ± 1.88 kg/pellet) and sodium lignosulfonate (198.1 ± 2.49 kg/pellet) pellets were weaker than those of bentonite (250.4 ± 2.06 kg/pellet ...
اقرأ أكثر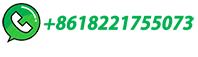
Usage of High-LOI Iron Ore Fines in Pellet Making
Loss on ignition (LOI) in the mineral represents the chemically bonded water which can be removed at high temperatures only. High LOI in iron ore fines has an adverse affect during pellet induration process. High-LOI iron ore fines are required for detailed laboratory pelletization studies and are used in pellet making. The received iron ore is martite–goethitic …
اقرأ أكثر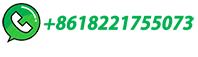
Pellet Plant produces Pellets using Iron ore and …
The location of a pelletizing plant affects the method of receiving raw materials such as iron ore, additives and binders. 2.2.1 Pre-treatment process of Iron Ore Fines In the pre-treatment process, iron ore fines are ground into finer size, suitable for green ball formation. Dry or wet grinding process is adopted for grinding the iron ore fines.
اقرأ أكثر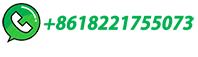
Characterization and Beneficiation of Dry Iron Ore Processing Plant …
JSW Steel Limited operates with a 4.2x2 Mtpa pellet plant and the production rate of each pellet plant is ~500t/hr. Pellet plant utilizes beneficiation plant (BP) product for pellet making. Beneficiation plant product size (pellet grade fines) is coarser (-45micron 40 to 45%) in nature.
اقرأ أكثر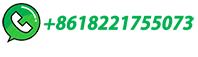
Cold briquetting of iron ore fines for DRI production: …
The objective of this research is to study the quality of blast-furnace iron ore pellets with binary basicity 1 fired on a pilot scale using the two main firing processes that are presently in use ...
اقرأ أكثر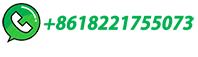
Iron Ore Agglomeration Processes and their Historical Development
These micro fines of high-grade concentrates had to be agglomerated for their use in the blast furnace and this has led to the development of the pelletizing process. ... Minnesota in 1952. The first iron ore pellet plant of the grate-kiln type was established at Humboldt Mine, Michigan in 1960. Allis-Chalmers (a predecessor company to ...
اقرأ أكثر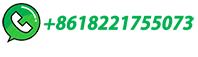
Iron Ore Pelletizing Process: An Overview | IntechOpen
This chapter aims to provide an overview and the evolution of iron ore pelletizing process including: Pelletizing process and raw materials. Balling technologies. Bonding …
اقرأ أكثر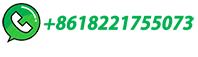
Understanding Pellets and Pellet Plant Operations
Iron ore pellets can be made from beneficiated or run of mine iron ore fines. ... These plants receive iron ore mostly by rails. some plant may receive by long distance slurry pipeline. In pelletizing plants located at port which are dependent on imported iron ore, the receiving method involves the transportation of the ore in a dedicated ship ...
اقرأ أكثر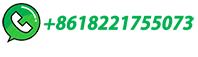
Characterization and Beneficiation of Dry Iron Ore …
Characterization and Beneficiation of Dry Iron Ore Processing Plant Reject Fines to Produce Sinter/Pellet Grade Iron Ore Concentrate P. Dixit1 & D. Makhija1 & A. K. Mukherjee1 & V. Singh1 & A. Bhatanagar2 & R. K. Rath3 Received: 6 September 2018 /Accepted: 12 September 2018 /Published online: 18 September 2018
اقرأ أكثر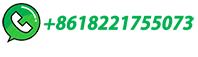
iron ore concentrate vs. pellets
Iron ore pellet plant in Iran. Thankfully, iron ore concentrate vs. pellets have enough export quality. The low percentage of impurities and harmful elements present in the product, making it popular in world markets, has boomed its export. ... Iron ore fines. The price of one ton of magnetite iron ore 60%, delivery of fob, is $ 55.2 per tonne ...
اقرأ أكثر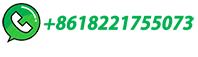
Pre-Feasibility Report
1.2 MTPA (2X0.6 MTPA) pellet plant, 2X350 TPD DRI plant (2,31,000 TPA sponge iron production) along with 16 MW (2X8 MW) WHRB and Induction Furnace (4X15 T) and CCM for production of 1,98,000 Ingots/Billets and 1,94,000 TPA TMT bars by M/s Grace Industries ... Thus, the iron ore fines so generated are utilized through pelletizing route for ...
اقرأ أكثر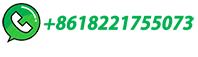
Cold briquetting of iron ore fines for DRI production
Fine and ultrafine iron ores have always been a challenging raw material to use in the blast furnace as well as in alternative ironmaking processes. Despite of having superior iron content than lumpy ores, their handling is very difficult. Traditional techniques like sintering and pelletizing have certain limitations in terms of particle size of fine ores as well as a maximum …
اقرأ أكثر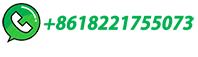
The Sintering Process of Iron Ore Fines – IspatGuru
The process of sintering begins with the preparation of the raw materials consisting of iron ore fines, fluxes, in-plant metallurgical waste materials, fuel and return fines of the sinter plant. These materials are mixed in a rotating pelletizing drum and water is added in order to reach proper agglomeration of the raw materials mix.
اقرأ أكثر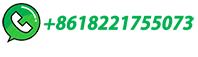
Beneficiation Plants and Pelletizing Plants for Utilizing …
- Fine: Ore fines have diameters of approximately 0.15mm to 10mm and are agglomerated by a sintering plant before being charged into a blast furnace. ... pelletizing plant. 1.2 Outline of iron ore production The production of iron and steel in China has increased dramatically. In response to the increasing
اقرأ أكثر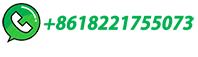
PMAI I Pellet Manufacturers Association of India
Pelletizing technology is an innovative way to produce pellet from iron ore fines which are mine's waste materials. Pellet is basically iron oxide ball which contains all types of properties. ... (KIOCL) set up the first 3 MTPA large scale pellet plant in Mangalore in 1987. Later on the capacity was increased to 4 million tons per year ...
اقرأ أكثر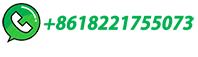
iron ore fines, lump and pellets
Keywords: Blast furnace pellets, sinter feed, iron ore fines, iron ore pellets, iron ore lumps. Telephone number: +51 1 330-7931 Fax number: +51 1 330-7931 ... a magnetic separation plant (iron ore grinding and concentration); a pelletizing plant; and export pier (a 300 metre pier) to service large vessels and (iii) administrative offices at ...
اقرأ أكثر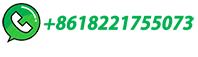
1.2 mtpa iron ore pellet plant | PPT
1. 1.2MTPA Iron Ore Pellet Plant Scada Overview Grate-Kiln technology. Grate Kiln process is unique process designed to evenly indurate pellets to increase its mechanical properties. This process employ a conventional 'Straight Grate' followed by a 'Rotary Kiln' designed to churn the pellets & thus increase even heating as well to avoid fragmentation in …
اقرأ أكثر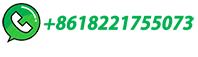